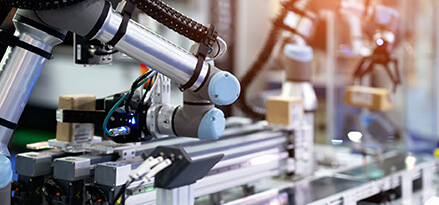
Manufacturing (Mobility)
No more off switch
How mobility is flipping the manufacturing model and putting the customer in control
According to the World Economic Forum, manufacturing accounted for 21% of ASEAN’s GDP in 2018. This represents a total of approximately US$670Bn, a figure they expect to reach US$1.4Tn by 20281. If manufacturers in the region fully embrace new technologies like IoT, 5G, robotics and edge compute, then this figure could climb even higher thanks to improved productivity gains and the creation of new revenue streams.
Critical to achieving a share of growth will be the ability of manufacturers to master the post-pandemic mobility challenge. To ensure that the supply of raw materials isn’t disrupted and the delivery of finished products to their customers isn’t compromised. Mobility used to be a simple concept in manufacturing. Simply a question of achieving a reliable means of getting goods from A to B quickly and cheaply. A highly commoditized service.
But so much has changed.
The pandemic revealed fault lines and amplified inadequacies in existing mobility solutions. Supply chains were shown not to be resilient. Over reliance on certain logistics partners or markets became painfully clear. Accepted ways of doing business were exposed as outdated.
“The pandemic also sparked new innovations in industrial mobility.”
The pandemic also sparked new innovations in industrial mobility. In part this innovation was driven by an urgent need to get goods into the hands of the people who needed them - both people living in remote rural areas and those hidden in increasingly crowded cities. But the innovation was also driven by opportunity. The opportunity to challenge business as usual and capitalize on a broad acceptance by manufacturers that only increased investment in digital transformation could secure a profitable future.
Manufacturers must reimagine their mobility strategy for a world where goods can move in faster, safer, more dependable and coordinated ways. Where cars, ships and planes can drive, sail and fly themselves. Where smart transportation systems can make sense of the urban chaos and close the rural divide. A world where customers and consumers expect to be better connected to the goods and resources they need or desire. In this context manufacturing’s mobility challenge is less ‘How do I get goods from A to B?’ and more ‘How do I provide partners and customers with on demand access and connectivity to different kinds of resources?’.
In fact, speed and accuracy of delivery could become such a point of difference that the lines blur between manufacturing and mobility. Rather than crafting mobility solutions to optimize supply and delivery, manufacturers need to adapt the production process to ensure they can capitalize on a potential mobility advantage.
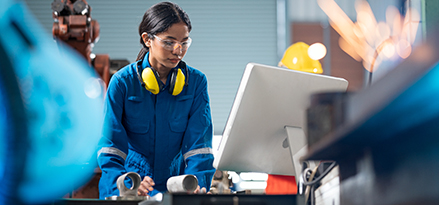
Imagine the banking sector as a parallel. Only a few years ago legacy banks could set the agenda. They could shape the relationship with customers to their advantage. But then the digitization of the industry flipped the model. Customers demanded a more flexible, more tailored service that was always there at the point of need.
Manufacturing is headed the same way. Organizations will win market share by embracing a service mindset with mobility. A mindset that encourages them to be more adaptable, more responsive and more customer centric.
They have to create a supply chain without an off switch.
To achieve this they will be reliant on real-time intelligence. Data that is generated on the factory floor, remotely at the edge and through partners to inform the evolution of both the operational model and the service offering. The greater value placed in data will instantly put the ‘big names’ on the back foot. Innovative, digital-first manufacturers - perhaps smaller, perhaps localized, perhaps more engaged with e-commerce partners - have an opportunity to compete.
This is particularly exciting in a region like Southeast Asia where the explosion in e-commerce - across B2B and B2C - has created a feverish appetite for on demand services. Companies looking to digitally disrupt categories currently weighed down by legacy inefficiencies are achieving huge funding and expanding rapidly. In time, customer-driven factories are likely to be the norm, not the exception, in a region that needs and wants new ways to meet the demands of the burgeoning middle class.
Talent, even as mobility solutions themselves become more autonomous, will play a big part. Manufacturers will have to shed those employees wedded to business as usual and bring on board digital natives dedicated to category disruption. High on the list will be plant managers and maintenance leads. Plant managers will now have to work at a faster pace in a less predictable environment. Quality, safety and cost will have to be maintained without compromising a new operating model that is dependent on flexibility and speed of delivery. Likewise maintenance leaders - across the full length of the supply chain - will be under greater pressure to ensure machine uptime without putting employees at risk or reducing total cost of ownership. Their mastery of data will enable predictive maintenance, ensure faster problem resolution and, as much as possible, reduce the strain on the vehicles and machines involved.
Mobil, as an expert in the mobility space, is determined to help our partners - leaders and teams - make the change. We are looking to provide manufacturers with the real-time data they need to make faster, more accurate decisions on maintenance and also simple services designed to enable a fast moving, flexible delivery service to their customers.
Citations
Sources
The sustainable mobility movement charges ahead digitally - World Bank, October 2021
Shaping the Future of Mobility - World Economic forum
Guide to Inbound and Outbound Logistics: Processes, Differences and How to Optimize - Oracle Netsuite
How to tackle lubrication problems in industrial manufacturing - Plant Engineering, July 2021
Industrial Mobility: How Autonomous Vehicles Can Change Manufacturing - The Manufacturing Institute, 2022
Mobility Solutions and Future of Manufacturing Industry - Demand Talk, August 2020
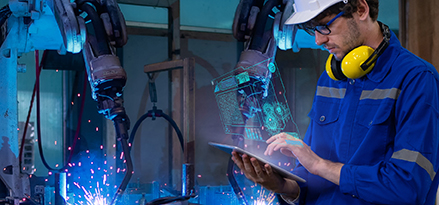
Related content
-
Expect the unexpected? Wouldn’t it be nice if you didn’t have to?
Advanced analytics help manufacturers stay ahead of the changing unknown and respond with the right action.
Learn more