Our leading-edge lubricants and unmatched industry expertise can help you advance the productivity of your power plants.
Mobil™ lubricants are designed to help power generation plants boost equipment reliability, lower operating costs, and extend machine life. We’re committed to helping your plant be more productive, so you can increase productivity while achieving environmental care and safety goals. Mobil™ industrial lubricants for power plants are engineered to perform even in the most extreme conditions, including high temperature and heavy load in wet, dusty conditions.
We can also help keep your critical equipment running more reliably and efficiently with Mobil℠ Engineering Services. Our Turbine Commissioning service can help you prepare your lubrication system timely startup and reliable operation after installation or overhaul. We can also provide advice on:
-
- Equipment troubleshooting
- Energy-saving options
No Time For Downtime
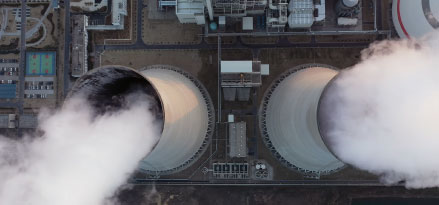
At Mobil™, we know how important uptime is for our power generation customers.
Light, heat, food, fun. Everything relies on turbines running smoothly and efficiently. It’s why we offer innovative products and services, as well as expert advice to help keep our customers running strong.
Mobil Bundle Builder Module:

Find Turbine Solutions with Mobil Bundle Builder
Use our Turbine Bundle Builder to get started on your own customized mix of Mobil™ products and services.
Technical Resource Module:
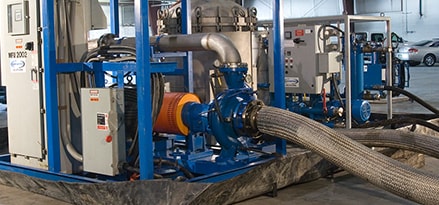
High Velocity Oil Flushing | Mobil™
The high velocity oil flushing service from Mobil℠ can help you boost equipment reliability and avoid costly downtime due to carbon and/or varnish/sludge buildup.
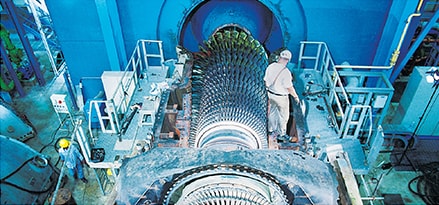
Turbine oil condition monitoring training guide | Mobil™
Help ensure long, trouble-free turbine operation with sound oil condition monitoring.