Maintaining uptime
To maximize profitability and growth by sustaining high production, wood pellet mills depend on reliable equipment performance. They need to minimize maintenance, repair and replacement costs, but due to the industry’s severe operating conditions, frequent bearing failures are common. Using the right grease is necessary to help keep equipment up and running.
Roller bearing temperatures in wood pellet mills often run continuously at 250°–300°F (120°–150°C), depending on ambient temperature, wood type and machine design. These temperatures put significant stress on the lubricating grease. Many greases fail, which can result in premature bearing failure.
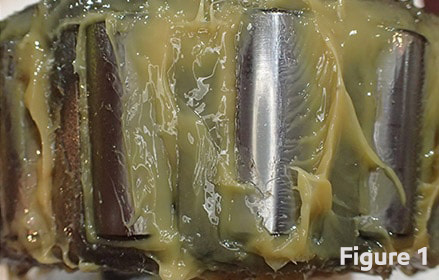
Additionally, the viscosity-thinning effects of high temperatures combine with the contaminants inherent in the pelleting process to create more challenges. Grease is used as a seal to keep out contaminants, but if the lubricant film ruptures or is bridged by contaminants, metal-to-metal contact can occur, causing bearing wear. To maintain the seal, OEMs set high feed rates. However, continually replenishing the grease can be expensive.
For wood pellet operations, ExxonMobil engineers often recommend Mobil Centaur™ calcium sulfonate greases to help protect bearings through:
- Excellent high-temperature bleed control
- High inherent extreme pressure (EP) protection
- Stay-in-place performance to reduce relubrication requirements
High temperature protection
Continuous high equipment temperatures can cause grease to release oil excessively. This oil escapes from the bearings, leaving them unprotected. It also leaves behind concentrated thickener in the bearings and feed lines, which can block new grease from reaching the bearings. Mobil Centaur greases maintain consistency by resisting high-temperature bleed and caking (Figure 1). This performance has been demonstrated in the Dropping Point Test (ASTM D2265).
Extreme pressure
To prevent bearing wear from metal-to-metal contact, Mobil Centaur greases provide exceptional EP protection, which is inherent in the calcium sulfonate thickener. In the 4-Ball EP Test, Mobil Centaur greases typically handle weld loads of 400 kg or higher.
Reduced grease consumption
Compared to standard lithium complex lubricants, Mobil Centaur grease allows for longer relubrication intervals — up to 50 percent in some models — which can help lower maintenance and product replacement costs.
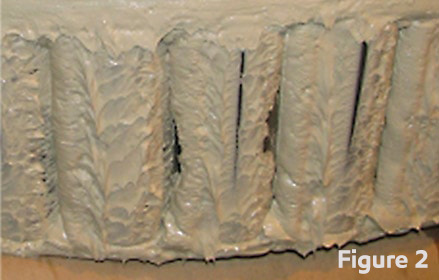
Additional properties
Mobil Centaur greases also provide outstanding water resistance, wet mechanical stability and corrosion protection. In the wet environments common in pellet mills, grease is used as a sealant. However, most greases soften when they absorb water, which can cause them to run out and leave bearings unprotected. Some greases designed to resist water absorption will maintain stability, but the water they leave in the bearing can lead to rust and corrosion.
Mobil Centaur greases are able to absorb water while maintaining consistency and adhesion (Figure 2). They have demonstrated this ability in ASTM D1264 (Water Washout Test) and ASTM D4049 (Water Spray Resistance Test).
Protecting productivity
To achieve their goals, wood pellet operations can rely on the unique capabilities of Mobil Centaur greases to help minimize bearing failure and maintain peak production and profitability.