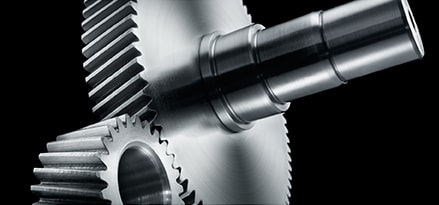
Mobilgear™ 600 XP Series gear oils
Gear Oil
Mobilgear™ 600 XP Series oils are formulated to help you stay ahead of the changing needs of gearbox technology.
Our Mobilgear™ 600 XP Series advanced technology lubricants are designed to protect gears, bearings and seals in all types of enclosed-gear drives with circulation or splash lubrication systems.
These gearbox oils are formulated for outstanding extreme-pressure characteristics and load-carrying properties in a broad range of industrial and marine equipment. Additionally, these oils help to reduce:
- Gear and bearing wear by protecting against micropitting
- Oil leakage through outstanding seal compatibility
- Unscheduled downtime due to excellent resistance to oxidation and thermal degradation
{0} offers {1} lubricant grades
<%= raw.productdescription%>
<%= raw.marketindustrialproducttypeandfeature %> <% } else { %> <%= title ? title : '' %>
<%= raw.productdescription%>
<%= raw.marketindustrialproducttypeandfeature %> <% } %>
Technical resources
Features and Benefits
Mobilgear 600 XP Series products are a leading member of the Mobil brand of industrial lubricants that enjoy a reputation for innovation and high performance capability. These mineral-based products are designed to provide high quality industrial gear oils, meeting the latest industry standards and with high versatility to lubricate a broad range of industrial and marine equipment.
Mobilgear 600 XP Series products offer the following features and potential benefits:
Features |
Advantages and Potential Benefits |
Enhanced gear wear protection from micropitting |
Less gear and bearing wear resulting in less unexpected downtime |
Reduced debris denting from generated wear particles |
Up to 22% improvement in bearing life reducing bearing replacement costs and improving productivity |
Improved bearing wear protection |
Improved bearing life resulting in higher productivity |
Outstanding compatibility with a range of seal materials |
Reduced leakage, oil consumption and contamination ingress helping to reduce maintenance, extend gearbox reliability and higher productivity |
Excellent resistance to oil oxidation and thermal degradation |
Helps extend lubricant life with lower lubricant and lubrication costs and reduced scheduled downtime. |
High resistance to sludge and deposit formation |
Cleaner systems and reduced maintenance |
Wide range of applications |
Fewer grades of lubricant required because of wide range of application, leading to lower purchase and storage costs and less danger of using wrong lubricant |
Optimised resistance to rust and corrosion of steel and corrosion of copper and soft metal alloys |
Excellent protection of machine parts, with reduced maintenance and repair costs |
Resistance to foaming and emulsion formation |
Effective lubrication and problem free operation in the presence of water contamination or in equipment prone to oil foaming |
Applications
Mobilgear 600 XP lubricants are used in a wide range of industrial and marine applications, especially spur, helical, bevel and worm gearing. Specific applications include:
• Industrial gearing for conveyers, agitators, dryers, extruders, fans, mixers, presses, pulpers, pumps (including oil well pumps), screens, extruders and other heavy duty applications
• Marine gearing including main propulsion, centrifuges, deck machinery such as winches, windlasses, cranes, turning gears, pumps, elevators and rudder carriers
• Non-gear applications include shaft couplings, screws and heavily loaded plain and rolling contact bearings operating at slow speeds.
Specifications and Approvals
This product has the following approvals: |
68 |
100 |
150 |
220 |
320 |
460 |
680 |
Bundeswehr TL 9159-0105 |
|
|
|
X |
|
|
|
Flender |
|
|
X |
X |
X |
X |
|
Renk B19828 300 |
|
X |
|
|
|
|
|
Renk B19828 400 |
|
|
X |
|
|
|
|
Renk B19828 600 |
|
|
|
X |
|
|
|
SEW-Eurodrive |
|
|
X |
X |
X |
X |
X |
ZF TE-ML 04F |
|
|
|
X |
|
|
|
ZF TE-ML 04H |
|
X |
X |
|
|
|
|
ZF TE-ML 27 |
|
X |
X |
X |
X |
X |
|
This product meets or exceeds the requirements of: |
68 |
100 |
150 |
220 |
320 |
460 |
680 |
AGMA 9005-F16 |
X |
X |
X |
X |
X |
X |
|
China GB 5903-2011, L-CKC |
|
|
|
|
|
|
X |
China GB 5903-2011, L-CKD |
|
X |
X |
X |
X |
X |
|
DIN 51517-3:2018-09 |
X |
X |
X |
X |
X |
X |
X |
ISO L-CKC (ISO 12925-1:2024) |
|
|
|
|
|
|
X |
ISO L-CKD (ISO 12925-1:2024) |
X |
X |
X |
X |
X |
X |
|
Properties and Specifications
Property |
68 |
100 |
150 |
220 |
320 |
460 |
680 |
Grade |
ISO VG 68 |
ISO VG 100 |
ISO VG 150 |
ISO VG 220 |
ISO VG 320 |
ISO VG 460 |
ISO VG 680 |
Copper Strip Corrosion, 3 h, 100 C, Rating, ASTM D130 |
1B |
1B |
1B |
1B |
1B |
1B |
1B |
Density @ 15.6 C, kg/l, ASTM D4052 |
0.88 |
0.88 |
0.89 |
0.89 |
0.9 |
0.9 |
0.91 |
EP Properties, Timken OK Load, lb, ASTM D2782 |
65 |
65 |
65 |
65 |
65 |
65 |
65 |
Emulsion, Time to 37 mL Water, 82 C, min, ASTM D1401 |
30 |
30 |
30 |
25 |
25 |
30 |
30 |
FE8 wear test, V50 roller wear, mg, DIN 51819-3 |
2 |
2 |
2 |
2 |
2 |
2 |
2 |
FZG Micropitting, Fail Stage, Rating, FVA 54 |
|
10 |
10 |
10 |
10 |
10 |
10 |
FZG Micropitting, GFT-Class, Rating, FVA 54 |
|
High |
High |
High |
High |
High |
High |
FZG Scuffing, Fail Load Stage, A/16.6/90, ISO 14635-1(mod) |
|
12+ |
12+ |
12+ |
12+ |
12+ |
12+ |
FZG Scuffing, Fail Load Stage, A/8.3/90, ISO 14635-1 |
12+ |
12+ |
12+ |
12+ |
12+ |
12+ |
12+ |
Flash Point, Cleveland Open Cup, °C, ASTM D92 |
230 |
230 |
230 |
240 |
240 |
240 |
285 |
Foam, Sequence I, Tendency/Stability, ml, ASTM D892 |
0/0 |
0/0 |
0/0 |
0/0 |
0/0 |
0/0 |
0/0 |
Foam, Sequence II, Tendency/Stability, ml, ASTM D892 |
30/0 |
30/0 |
30/0 |
30/0 |
30/0 |
30/0 |
30/0 |
Four-Ball Extreme Pressure Test, Load Wear Index, kgf, ASTM D2783 |
47 |
47 |
47 |
48 |
48 |
48 |
48 |
Four-Ball Extreme Pressure Test, Weld Load, kgf, ASTM D2783 |
200 |
200 |
250 |
250 |
250 |
250 |
250 |
Kinematic Viscosity @ 100 C, mm2/s, ASTM D445 |
8.8 |
11.2 |
14.7 |
19.0 |
24.1 |
30.6 |
39.2 |
Kinematic Viscosity @ 40 C, mm2/s, ASTM D445 |
68 |
100 |
150 |
220 |
320 |
460 |
680 |
Pour Point, °C, ASTM D97 |
-27 |
-24 |
-24 |
-24 |
-24 |
-15 |
-9 |
Rust Characteristics, Procedure B, ASTM D665 |
PASS |
PASS |
PASS |
PASS |
PASS |
PASS |
PASS |
Viscosity Index, ASTM D2270 |
101 |
97 |
97 |
97 |
97 |
96 |
90 |