By Wayne Scraba, automedia.com
The spark plug is a seemingly simple device, although it is tasked with a couple of different but critical jobs. First and foremost, it creates (literally) an artificial bolt of lightning within the combustion chamber (cylinder head) of the engine. The electrical energy (voltage) it transmits is extremely high in order to create a spark and to “light the fire” within the controlled chaos of the combustion chamber. Here, the voltage at the spark plug can be anywhere from 20,000 to more than 100,000 voltage.
Thermal performance spark plugs
Although it initiates the spark to create combustion, the spark plug doesn’t sustain it. It does help to transmit heat out of the combustion chamber into the water jacket of the cylinder head.
The ability of a spark plug to dissipate heat from the combustion chamber is defined by the spark plug “heat range.” The temperature of the firing end of the spark plug must be maintained at a level high enough to prevent fouling, but low enough to prevent pre-ignition. Spark plug manufacturers refer to this as “thermal performance.” Thermal performance, or heat range of the spark plug, has nothing to do with the amount of energy transferred from the ignition system through the spark plug. Spark plug heat range is the area in which the spark plug functions thermally.
Cold spark plugs versus hot spark plugs
“Cold” spark plugs normally have a short heat flow path. This results in a very quick rate of heat transfer. Additionally, the short insulator nose found on cold spark plugs has a small surface area, which does not allow for a massive amount of heat absorption.
On the other hand, “hot” spark plugs feature a longer insulator nose as well as a longer heat transfer path. This results in a much slower rate of heat transfer to the surrounding cylinder head (and consequently, the water jacket).
The heat range of the spark plug must be carefully selected in order to create optimal thermal performance. If the heat range is not correct, you can expect serious trouble. Typically, the appropriate firing end temperature is (approximately) 900-1,450 degrees. Below 900 degrees, carbon fouling is possible. Above it, overheating becomes an issue.
Spark plug voltage rise
In terms of operation, the spark plug is connected to the high voltage generated by an ignition coil (by way of a conventional distributor or by way of an electronic means). As electricity flows from the coil, a voltage difference develops between the center electrode and ground electrode on the spark plug.
Because of the spark plug “gap,” coupled with the air/fuel mixture (which acts as an insulator) within the gap, the spark plug cannot immediately fire.
As the voltage rise increases to approximately 20,000 volts, the gap within the spark plug can be “breached” and it fires. With a spark plug removed from the cylinder head and properly grounded to fire, you can hear a definitive click. If conditions are dark enough, you can see the spark.
The click you hear is essentially a miniature clap of thunder, and the spark you observe is similar to a miniature form of lightning.
Within the combustion chamber, the intense heat created by the spark plug creates a small fireball within the gap. The fireball or combustion “kernel” expands and the cylinder (at least in theory) experiences complete combustion.
Spark plug construction
In terms of construction, spark plugs may not be quite as simple as you think. In fact, they are precision pieces of equipment.
Thanks to the folks at Champion Spark Plug, we can provide you with a complete breakdown of the various plug features. Keep in mind that the vast majority of spark plugs offer similar (although not necessarily identical) construction.
In the accompanying photos, you can see what many of the above spark plug features actually look like. Check them out.
Ribs: Insulator ribs provide added protection against secondary voltage or spark flashover and also help to improve the grip of the rubber spark plug boot against the plug body.
The insulator body is molded from aluminum oxide ceramic. In order to manufacture this part of the spark plug, a high-pressure, dry molding system is utilized. After the insulator is molded, it is kiln-fired to a temperature that exceeds the melting point of steel. This process results in a component that features exceptional dielectric strength, high thermal conductivity and excellent resistance to shock.
Insulator: The insulator body is molded from aluminum oxide ceramic. In order to manufacture this part of the spark plug, a high-pressure, dry molding system is utilized. After the insulator is molded, it is kiln-fired to a temperature that exceeds the melting point of steel. This process results in a component that features exceptional dielectric strength, high thermal conductivity and excellent resistance to shock.
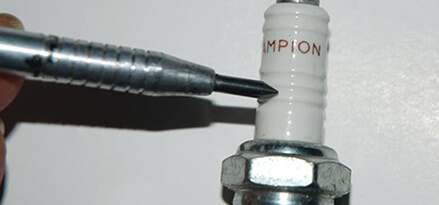
The pointer shows the spark plug insulator. As mentioned above, it is formed from aluminum oxide ceramic. The outer surface is ribbed to provide grip for the spark plug boot and to simultaneously add protection from spark flashover (crossfire).
Hex: The hexagon provides the contact point for a socket wrench. The hex size is basically uniform in the industry and is generally related to the spark plug thread size.
Shell: The steel shell is fabricated to exact tolerances using a special cold extrusion process. Certain types of spark plugs make use of a steel billet (bar stock) for shell construction.
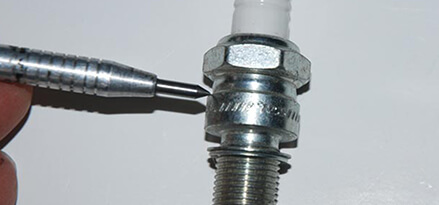
Plating: The shell is almost always plated. This enhances durability and provides for rust and corrosion resistance. The steel shell is fabricated to exact tolerances using a special cold extrusion process or, in other specialized cases, machined from steel billet. The hexagon machined onto the shell allows you to use a socket wrench to install or remove the plug.
Gasket: Certain spark plugs use gaskets while other examples are “gasketless.” The gasket used on spark plugs is a folded steel design that provides a smooth surface for sealing purposes. Gasketless spark plugs use a tapered seat shell that seals via a close tolerance incorporated into the spark plug.
Threads: Spark plug threads are normally rolled, not cut. This meets the specifications set forward by the SAE along with the International Standards Association.
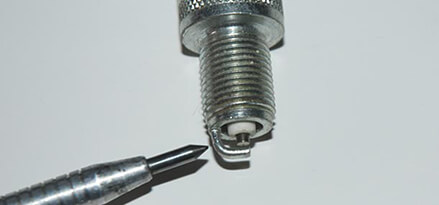
Ground electrode: There are a number of different ground electrode shapes and configurations, but for the most part, they are manufactured from nickel alloy steel. The ground electrode must be resistant to both spark erosion and chemical erosion, both under massive temperature extremes.
Center electrode: Center electrodes must be manufactured from a special alloy that is resistant to both spark erosion and chemical corrosion. Keep in mind that combustion chamber temperatures vary (and sometimes radically). The center electrode must live under these parameters.
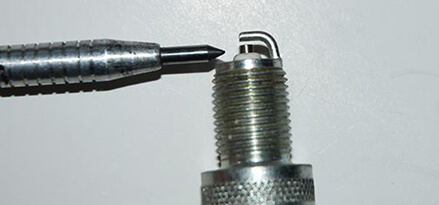
Spark park electrode gap: The area between the ground electrode and the center electrode is called the gap. Center electrodes must be manufactured from a special alloy that is resistant to both spark erosion and chemical corrosion.
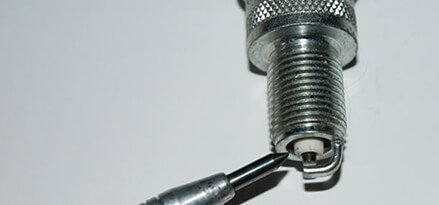
Insulator nose: There are a large number of insulator nose shapes and sizes available, but in essence, the insulator nose must be capable of shedding carbon, oil and fuel deposits at low speeds. At higher engine speeds, the insulator nose is generally cooled so that temperatures and electrode corrosion are reduced.